Wirtgen Milling Machine Operating Instructions and Precautions
Donec ultrices tincidunt arcu non sodales.
The proper use of tools is a critical part of the operation of a milling system. As the depth of milling increases, the contact time between the cutter and the material is extended, which leads to increased frictional heating. In order to prevent damage to the carbide tip of the cutter due to thermal erosion, it is necessary to increase the amount of water sprayed to cool the cutter head at the right time. When the milling depth is shallow (below 6cm), the amount of water spray should be reduced to facilitate the smooth output of the material, thus reducing the direct contact between the tool and the material being milled, and thus reducing the wear rate of the tool.
To ensure efficient and safe milling operations, the rotational condition and wear of the cutter should be checked regularly. It is recommended that a thorough inspection be carried out every 6-8 hours of work. During the inspection, pay special attention to whether the cutter can rotate freely in the cutter holder, so as to detect and deal with any abnormalities in a timely manner.
When the tool is badly worn, it must be replaced promptly. During the replacement process, try to maintain the consistency of the tool’s extended length to ensure the stability and efficiency of the milling operation. If part of the milling cutter has been worn to 1/2 and needs to be replaced, it is recommended to replace the whole set and reassemble the less worn cutter to prolong its service life and ensure the quality of pavement construction.
1. Reasonable regulation of milling speed
The working speed and rotor speed of a road milling machine are its core technical indexes, which are directly related to the productivity of the machine. These speed parameters will be affected by multiple factors such as pavement material, asphalt mixture hardness, milling depth ambient temperature, etc. Therefore, they are usually designed to be infinitely adjustable to adapt to the operational requirements under different working conditions.
For common asphalt pavement, the relationship between the working speed of the pavement milling machine and the milling depth presents certain characteristics, as shown in the figure. This relationship characteristic will change accordingly with the different pavement materials and the change in ambient temperature.
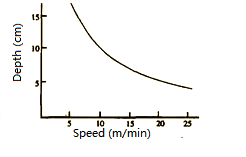
2. Belt protection measures
The take-up belt of a milling machine is responsible for receiving the material milled by the cutter. In order to prevent wear and tear of the belt caused by loose material, as well as to ensure sealing of the rotor space and limiting the particle size of the milled old material, and the reliability of the belt’s receipt and avoiding additional knocks, measures can be taken to install belt boots and grade control beams. By regularly inspecting and replacing the belt boots and combining them with a reasonable grade control program, the belt can be effectively protected and wear can be reduced, thus building a stable and reliable material receiving system.
3. Importance of regular cleaning
The cleanliness of machinery is critical to its operational reliability. If the system is mixed with dirt or sharp solid particles, failures such as friction, clogging and jamming may occur at any time, and even lead to seal leakage and temperature rise, which in turn leads to a series of chain reactions. Therefore, in the daily use of pavement milling machinery, regular cleaning is particularly important. This is not only about the neat appearance of the machinery, but also the key to ensuring its safe and stable operation.
4. Enhanced maintenance and upkeep
During operation, the milling machine will be affected by vibration and alternating loads, resulting in the loosening of many bolts. In order to ensure the safe and stable operation of the machinery, these bolts must be checked and tightened regularly to prevent the occurrence of faults such as oil leakage, air leakage, water leakage, and electricity leakage. At the same time, it is also necessary to check and adjust the relative relationship and working parameters of many parts on the pavement milling machine to ensure that the machinery can work normally and safely. These adjustments include clearance, stroke, angle, pressure, flow, tightness, and track shift.
With the modernization and development of the road transportation industry, mechanized maintenance methods have gradually become the new standard of the industry. The maintenance equipment with a milling machine as the core is widely used on many highways in the country. With the approaching of the highway overhaul period and the deepening of the understanding of modernized maintenance methods, the application of pavement milling machines will be more widely used. Therefore, scientific use and reasonable maintenance of pavement milling machines to give full play to their maximum efficacy are of great significance to improving construction quality and efficiency and reducing construction costs.
Of course, construction machinery will inevitably have a variety of problems in the course of use. Timely replacement of damaged and non-functional parts is also crucial. As a supplier with more than ten years of spare parts application and sales, we have rich experience in the sales of WIRTGEN, BOMAG, VOLVO, DYNAPAC , and other brands of spare parts or aftermarket parts, and can provide customers with perfect service. If you have construction machinery parts needs, please contact us.
Viverra nibh cras pulvinar mattis nunc sed blandit. Aliquet eget sit amet tellus cras adipiscing enim. Rutrum quisque non tellus orci ac auctor augue mauris. Maecenas volutpat blandit Viverra orci sagittis eu volutpat odio facilisis mauris sit. Facilisi cras fermentum odio eu feugiat pretium. Aliquam purus sit amet luctus. Euismod quis viverra nibh cras. Sed faucibus turpis in eu mi bibendum. Turpis tincidunt id aliquet risus feugiat in ante.